In the world of industrial operations, the reliability of equipment is of utmost importance. However, one crucial component that is often overlooked is the integrity of flexible industrial cables. These cables are the lifelines of many operations, as they carry power and signals across various machinery and systems.
To prevent downtime, ensure safety, and maintain productivity, it is essential to ensure their quality through rigorous testing and validation processes. Flexible industrial cables are subjected to harsh conditions, from extreme temperatures to constant movement and flexing. They must endure a multitude of challenges without compromising performance. Rigorous testing protocols are employed to assess their durability under various stressors. Let’s take a look at some of the various tests and validation methods we recommend for your industrial flexible cable.
Flexible Cable Tests
Mechanical Testing: Evaluating Flexibility and Strength
One of the primary aspects of testing flexible industrial cables is assessing their mechanical properties. This includes evaluating their flexibility, bend radius, and tensile strength. Cables must withstand repeated bending and flexing without succumbing to fatigue or breakage. Mechanical tests simulate real-world conditions to ensure cables can withstand the demands of industrial environments.
Mechanical Testing Equipment
- C-Track Tester: Simulates the movement a cable sees while installed in a Cable Carrier or “Cat Track”. It is used to verify the performance of the cable to resist the stress caused by continuous bending. This type of cable stress occurs in all Chain-Track applications.
- Torsional Tester: Used to verify the performance of the cable to resist the stress caused by a clockwise and counterclockwise twisting force. This type of cable stress occurs in automation and robotic applications.
- Tick-Tock Tester: This tool is used to verify the performance of the cable in resisting the stress caused by dynamic flexing and bending applications, which occur in automation and robotic applications.
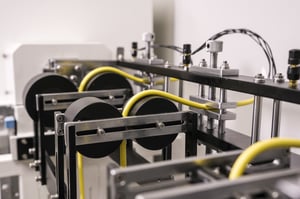
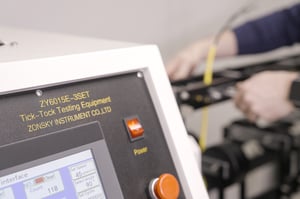
- Tensile Tester: Measures the maximum force a cable can withstand before it fails. This test evaluates the tensile strength of cables, ensuring they can endure the stresses of installation and operation.
- Abrasion Tester: Used to verify the ability of the cable to last when exposed to abrasive forced based on mass loss. This type of cable stress occurs in mining and welding applications or anytime the cable is being dragged or run over.
Electrical Testing: Ensuring Proper Conductivity and Insulation
In addition to mechanical testing, the electrical performance of flexible cables is also evaluated. Conductivity tests verify that cables can efficiently transmit power and signals without loss or interference. Insulation resistance tests assess the integrity of insulation materials, ensuring protection against electrical faults and hazards. Comprehensive electrical testing guarantees the reliability and safety of flexible industrial cables.
Electrical Testing Instruments
- Insulation Resistance Testers: Insulation resistance testers measure the electrical resistance between a cable's conductors and its insulation. This test verifies the effectiveness of insulation materials in preventing electrical leakage and faults.
- Continuity Testers: Continuity testers check for uninterrupted electrical pathways within cables. This ensures proper connectivity and conductivity throughout the cable's length, which is crucial for reliable signal transmission.
- High Voltage Testers: High voltage testers assess a cable's ability to withstand high voltage levels without breakdown or insulation failure. These tests simulate extreme conditions to ensure cables remain safe and reliable under voltage stress.
Environmental Testing: Evaluating Performance in Extreme Conditions
Industrial settings can expose cables to a wide range of environmental factors, including temperature extremes, moisture, chemicals, and UV radiation. Environmental testing subjects cables to these conditions to assess their performance and longevity. Cables undergo accelerated aging tests to simulate years of exposure in a condensed timeframe, allowing manufacturers to identify potential weaknesses and make improvements.
Environmental Testing Chambers
- Temperature Chambers: Temperature chambers subject cables to extreme heat or cold to evaluate their performance under different temperature conditions. They can also cycle between high and low temperatures to simulate outdoor weathering. This helps determine the cable's thermal stability and resistance to temperature-related degradation.
- Humidity Chamber: Simulate high-humidity environments to assess the effects of moisture on cable materials. This is vital for applications where cables may be exposed to damp or humid conditions.
- Salt Spray Chamber: Create corrosive environments to test the corrosion resistance of cable materials, which is particularly important for cables installed in marine or coastal areas.
- UV Chamber: Expose the cable jacketing to continuous ultra-violet radiation to simulate long term exposure to sunlight. Poor UV resistant material will exhibit color fading, cracking, embrittlement, and loss of mechanical properties.
Quality Assurance and Certification
Once testing is complete, flexible industrial cables that meet stringent quality standards are certified for use in various applications. Certifications such as UL, CSA, MSHA, RoHS, and CE signify compliance with industry regulations and specifications, providing assurance of quality and reliability to end-users. Regular audits and inspections further ensure that manufacturing processes maintain consistency and uphold the highest standards.
Validation Methods
In the manufacturing and application of industrial flexible cables, various validation methods are crucial to ensure performance, safety, and compliance with relevant standards.
- Comparative Analysis: Manufacturers often validate new cable designs or materials by comparing them to existing standards or benchmarks. This ensures that any improvements or changes meet or exceed industry expectations.
- Field Testing: Field testing involves installing cables in real-world environments to assess their performance over an extended period. Feedback from field tests helps refine designs and identify any issues that may arise in practical applications.
- Certification and Compliance Testing: Seeking certification from regulatory bodies such as UL, CSA, or CE involves rigorous testing to ensure compliance with industry standards and regulations. Certification provides third-party validation of a cable's quality and safety.
Conclusion
Testing and validating flexible industrial cables are critical steps in ensuring industrial systems' reliability, safety, and performance. By subjecting cables to rigorous mechanical, electrical, and environmental testing, manufacturers can identify potential issues early and deliver products that meet the demanding requirements of modern industrial operations. Quality assurance processes and certifications provide confidence to users, knowing that their equipment is supported by cables that have been thoroughly tested and validated for optimal performance.