Welding is important in the shipbuilding process because it can create joints that are water and oil-tight. As you can imagine, a strong weld is essential to the integrity of the ship. On one large ship, it can have hundreds of joints that require welding.
Shipbuilders face many challenges in the shipyard that could prevent progress and create downtime during operation. The need for durable equipment and an experienced welder that can address the demands of different applications is vital. Gaining the best results is all about having the right equipment and right person for the job, so it’s important to assess the application and choose your equipment and professional accordingly.
An Educated Welder
Welding is one of the most critical operations within ship construction. When a weld fails, often the entire structure fails. After years of research and development in the field of welding, welders have been provided with fabrication processes that are automated and can produce consistent welds reliably. Since welding is such a critical process in shipbuilding, a welder must possess several certifications before starting their career. Not only should your welder be certified in shipbuilding weld processes but they should also understand safety requirements. The shipyard environment presents special challenges and potential hazards that welders need to be aware of. Any potential welder should study and understand the guidelines outlined in OSHAs Shipyard Industry Standards before beginning any on the job training, regardless of how much welding experience or certification that they have.
Reliable & Durable Weld Equipment
Once a shipyard has found certified welders for shipbuilding, providing reliable equipment is the next step. The most common types of welding used in shipyards are arc welding, gas welding, and resistance welding. These techniques have different requirements, but they all require a weld cable. A reliable and durable weld cable will allow an educated welder to successfully create proper welds during shipbuilding. In a shipyard, these cables are dragged from one area of the yard to the next experiencing heavy impact from rocks, sharp edges, and many other abrasive surfaces as they are moved around. Cuts in a weld cable jacket can expose the copper stranding and if exposed to metal in the ship it can cause arc-strike when the machine in energized. Arc strikes can cause cracking or fracturing which could result in catastrophic consequences.
Not only is the weld cable subject to abrasion from pulling and moving the cable around to each project area, but it is also exposed to the natural elements. Shipyards are exposed to rain, freezing temperatures, sunlight, and extreme heat. Having a power cable that is UV resistant, tested in extreme operating temperatures, and resistance to water and chemicals allows for a reliable cable for shipyard welding.
With the proper welding professional and reliable weld equipment, a shipbuilder can maximum productivity, quality, and safety at their shipyard and build a reliable vessel.
The TPC Welding Cable Solution
TPC has prided itself in developing welding cable designed for shipyards that will outperform other commercial welding cable in the market. There are several features that make TPC’s welding cable superior- the jacket material and its thickness, a fabric serve, and very fine copper stranding.
- Specially Compounded TSE Jacket is 25% thicker than ordinary welding cable jackets, giving exceptional damage resistance from chemicals, abrasion, oils, impact, weld splatter, tearing, open flame and heat.
- 100% Fabric Serve prevents shrink-back and improves tear resistance.
- 2-1/2 Times More Copper Stranding than conventional welding cable, allowing for maximum flexibility and ease of use.
- Available in custom colors and customizable print that can include the yard or facility name on the cable.
TPC has seen great success for their shipyard customers using Super-Trex® 600 Volt welding cable. A Rhode Island based company was experiencing weld cable failure every 3 months from exposure to moisture and weather.
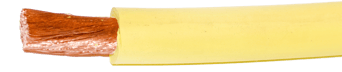
Not only was the cable compromised by the elements, it was also often run over by other vehicles and equipment in the yard. Each time a cable assembly failed, the cost to replace it was hundreds of dollars in replacement product plus labor – not to mention the cost of lost time and progress on projects! Read our case study and learn how TPC saved the customer $286,000 in 2 years!
TPC’s welding cable assembly saved the customer $286,000 in 2 years. Imagine the savings possible with your weld machines, contact us today!