Welding is a fabrication process that joins materials, usually metals, by using high heat to melt the parts together and then allowing them to cool, causing fusion. Welding is popular in several industries including shipbuilding, automotive, aerospace, and building and construction. Each industry has different demands when it comes to welding so understanding the project needs and proper welding techniques will better prepare you for a successful weld.
SAFETY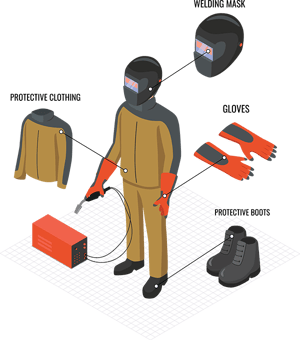
It’s important to understand the safety requirements for welding. Whether welding is conducted regularly in a facility or only for occasional projects, it’s essential to stay current with safety regulations and proper personal protective equipment (PPE) requirements.
A welding helmet, or also known as a hood, not only protects the welder’s face from sparks but also potentially vision-damaging ultraviolet and infrared rays emitted by the arc. The use of welding gloves, along with flame-retardant aprons, sleeves, and jackets are necessary to protect against flying sparks and flash burn. Avoid clothing that has cuffs or pockets that could potentially catch sparks. While the hood protects a welder’s face, it’s also important to have respiratory protection. Welding fumes contain vaporized metal which can lead to serious health problems if exposed. Welding boots, similar to protective clothing, need to be flame-retardant and have cover laces. Proper welding boots will protect your feet from sparks, corrosive materials on floor and hot molten metal spills.
Incorporating these safety considerations into your project will help keep you from becoming another injury statistic. For more information regarding welding safety, visit the American Welding Society (AWS), OSHA, or the National Institute for Occupational Safety & Health (NIOSH).
PROJECT LAYOUT
Once you have your safety gear together, next you must evaluate your project. Understand your objectives and specifications so you can better prepare for any challenges. Will you be in an unusual position or in a challenging environment? What type of welding is required to perform the job successfully? Different welding processes are better suited for use on different materials or in different circumstances. Understanding different welding processes is vital to the success of the project. Each welding process comes with their own set of pros and cons, so be sure to understand your project in its entirety before beginning.
Welding pROCESSES
Shielded Metal Arc Welding
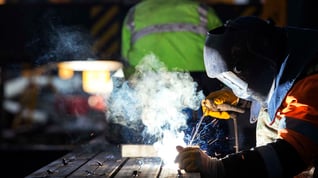
Shielded metal arc welding (SMAW), frequently referred to as stick welding, is a very common and popular method of welding. It is typically used in construction, steel fabrication, pipeline work and for repairing heavy equipment. It is a manual arc welding process that uses a consumable electrode covered with a flux, or a shielding agent to lay the weld. In simpler terms, a filler material melts to form a weld pool, which solidifies to join separate metal sections.
Gas Metal Arc Welding
Gas metal arc welding (GMAW) is an arc welding process which produces the merging of metals by heating them with an arc between a continuously fed filler metal electrode and the metal piece your working on. This process uses shielding from an externally supplied gas to protect the molten weld pool. GMAW is commonly known as MIG (Metal Inert Gas) welding and it is less commonly known as MAG (Metal Active Gas) welding.
Compared to SMAW, both use a consumable material known as the electrode to create the weld and the electrode must be protected from oxidizing forces during the welding process for a successful weld. SMAW encases the electrode in a layer of material known as flux. As the electrode melts, the flux turns to a gas that forms a protective layer around the molten weld pool. GMAW has no layer of flux. Instead, the consumable electrode feeds through a tool known as the spool gun. Not only does the spool gun guide the location of the electrode, but its tip also contains holes that emit a special shielding gas. The shielding gas covers the molten electrode as it pools onto the weld surface, protecting it from oxidation.
Flux Cored Arc Welding
Fluxed cored arc welding (FCAW) requires a continuously-fed consumable tubular electrode containing a flux and a constant-voltage. The flux itself is relied upon to generate the necessary protection from the atmosphere, producing both gaseous protection and liquid slag protecting the weld. The process is popular in construction because of its high welding speed and portability. As compared to SMAW and GTAW, there is less skill required to perform this weld.
Gas Tungsten Arc Welding
Gas tungsten arc welding (GTAW) is an arc welding process that uses a non-consumable tungsten electrode to produce the weld. The weld area and electrode are protected from oxidation or other atmospheric contamination by an inert shielding gas. GTAW is commonly used to weld thin sections of metal such as steel and aluminum. This welding process gives the operator better control over the weld compared to SMAW and GMAW, allowing for stronger, higher quality welds. However, GTAW is more complex and difficult to learn and is significantly slower than most other welding techniques.
Electron Beam Welding
Electron beam welding is a fusion welding process in which a beam of high-velocity electrons is applied to two materials to be joined. The metals being worked on melt and flow together as the kinetic energy of the electrons is transformed into heat upon impact. Electron beam welding is performed in a vacuum environment as the presence of gas can cause the beam to scatter. Due to the vacuum process and the high voltages used, this welding method is heavily automated and computer controlled. This welding process is a very precise and is also highly repeatable. The downside to this technology is the expensive cost and it requires frequent maintenance.
Atomic Hydrogen Welding
Atomic Hydrogen Welding (AHW) is a welding process in which welding is done using the arc produced between two tungsten electrodes and hydrogen gas provided by a hydrogen gas cylinder. It is named atomic hydrogen welding because the arc disassociates the hydrogen into atomic form. This process is also known as atomic arc welding.
The main difference between the AHW process and other welding processes is unlike AHW, in the other welding processes the arc is formed between the electrode and base metal. In the AHW process, the arc is formed between two electrodes.
Plasma Arc Welding
Plasma arc welding (PAW) is an arc welding process similar to GTAW. The electric arc is formed between an electrode and the piece of metal you are working on. The key difference from GTAW is that in PAW, the electrode is positioned within the body of the torch, so the plasma arc is separated from the shielding gas.
The main disadvantages of PAW compared to GTAW are the complexity of the equipment and the cost.
When trying to select the right welding process, be sure to take everything into account. Understand the metals you are working with, the location of the weld, your environment, how quickly the job needs done are all factors that will help you select the correct welding process.
TPC's wELDING solution
TPC has prided itself in developing welding cable that will last longer than any other commercial welding cable in the market, typically lasting over a year before needing replaced. What sets TPC welding cable apart from the rest?
Proprietary TSE Cable Jacket is 25% thicker than ordinary welding cable jackets, giving exceptional damage resistance from chemicals, abrasion, oils, impact, ozone, splatter, tearing, open flame and heat.
Proprietary Fabric Serve Insulation prevents shrinkage and provides an insulation system that resists oils, coolants, acids, and chemicals.
2-1/2 Times More Copper Stranding than conventional welding cable, allowing for maximum flexibility and movement within the jacket.
TPC offers several configurations of 600 Volt cable that remain flexible and outlast commodity welding cables in a variety of welding and power applications.